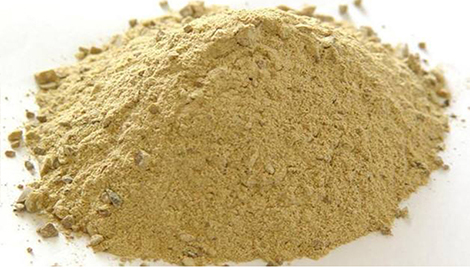
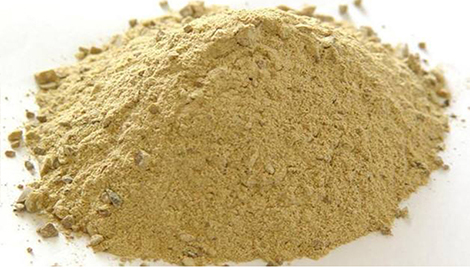
Refractory fire Ramming Mass
Model Number:
Certification:
Minimum Order Quantity:
Currently, there are two type of ramming masses used in the glass furnace. One is AZS ramming mass and the other is zirconite ramming mass.
AZS ramming mass is made of crushed fused cast AZS brick particles as aggregate materials mixed with other auxiliary materials. It reserves the advantage of fused cast AZS bricks such as good corrosion resistance to molten glass and metals, low porosity and stable properties.
Zirconite ramming mass is made by adding a certain portion of crushed sintered zircon brick particles into the zircon clay and then adding other auxiliary materials. It has high refractoriness and good corrosion resistance to glass liquid.
During construction, the two types of zircon ramming masses are mixed by adding a proportion of water. After mixed evenly, the ramming mass is wet and loose. Then it is rammed and sintered into a rigid unitary body. It contains no phosphoric acid and is safer and more convenient.
Although the two zircon ramming masses both have good corrosion resistance to molten glass and almost no pollution to glass liquid, proper choice should be made according to the properties of the glass produced.
The main difference between the two ramming masses is the content of Al2O3 and the porosity. Since there are joints between the paving bricks, glass liquid will penetrate into the ramming mass through the joints. Therefore, the ramming mass should have good corrosion resistance to the molten glass.
AZS ramming mass can form a layer of Al2O3 layer when contacting the alkali glass liquid, which prevents ramming mass from melting in the glass liquid. The interface layer has passivation characteristics and it has good abrasive resistance and corrosion resistance. Since zirconite ramming mass contains no alumina, when it contacts alkali glass liquid, it will not form a protective layer. So, it is easy to be broken down.
In short, the two have similar corrosion resistance. Since zirconite ramming mass has a content of Al2O3 and two have different porosity, AZS ramming mass is suitable to the bottom ramming layer of soda-lime-silica glass, vacuum glass and other alkali glass furnaces, while zirconite ramming mass is more suitable to the bottom ramming layer of weak alkaline borosilicate glass furnaces.
Ramming Mass:
1. High refractoriness, High refractoriness under load.
2. High density, low porosity.
3. Good slag resistance and corrosion resistance.
4. High strength and wear resistance.
5. Good resistance to flake performance.
6. Good thermal shock stability.
7. Scouring resistance
8. Good hot strength.
Ramming Mass Technical Date:
Item | Behaviors | ||||
AZSR-50V ERSOL 50 | AZSM-06J ERSOL 06 | AZSM-05 ERSOL 05 | AZSM-04L ERSOL 04 | ||
Chemical Composition | Al2O3 | 48 | 48 | 48 | 48 |
ZrO2 | 30 | 30 | 30 | 30 | |
SiO2 | 20 | 20 | 20 | 20 | |
Others | 2 | 2 | 2 | 2 | |
Bulk density g/cm3 | 3.2 | 3.1 | 3.1 | 3.1 | |
Crystallographic analysis after being sintered at 1300/1500°C | Corundum, zirconium oxide | Corundum, zirconium oxide | Corundum, zirconium oxide | Corundum, zirconium oxide | |
Thermal conductivity | Good | Good | Good | Good | |
Anti-corrosion property | Excellent at 1300°C | Excellent at 1300°C | Excellent at 1300°C | Excellent at 1300°C | |
particle diameter of grain | 0-5mm | 0-0.6mm | 0-0.5mm | 0-0.4mm | |
Application temperature | Cold/low temperature | Cold/low temperature | Cold/low temperature | Cold/low temperature | |
Quantity of water | 8-10% (proportion by weight) | 10-12% (proportion by weight) | 10-12% (proportion by weight) | 10-12% (proportion by weight) | |
Solidification | Water (ceramic) | Water (ceramic) | Water (ceramic) | Water (ceramic) | |
Packaging | 25kg/bag | 25kg/bag | 25kg/bag | 25kg/bag | |
Quality guarantee period | 12 months | 12 months | 12 months | 12 months | |
Used for | Under bottom paving, spreading, Melting end and working area | Under bottom paving, spreading and the place between fused cast brick and ERSOL 50 | Under bottom paving, spreading, and the joint between bricks of two layers that are between the fused cast brick and ERSOL 50 | Joint between bricks of two |
Production capacity: Our factory actively response to government environmental protection policy, we designed and built the fully automatic controlled high temperature gas tunnel kiln (1700℃), and got capacity of annual output 70,000 tons of high quality refractory products.



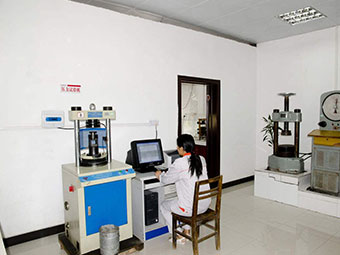
Packing details:
★Bricks: Fumigated wooden pallet with log paperboard covered and stainless steel band strapping, the whole outside is wrapped with thermoplastic film. Or carton packaging.
★Wooden pallet size: usually 92*92cm (standard brick)
★Castable: Ton bag with rain film and 25kg bags inside
★Or according to customer’s requirements
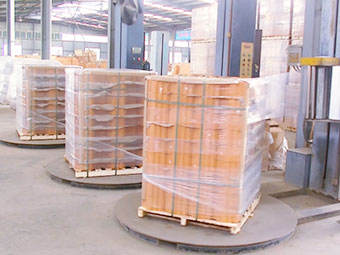
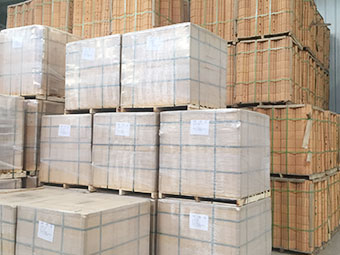
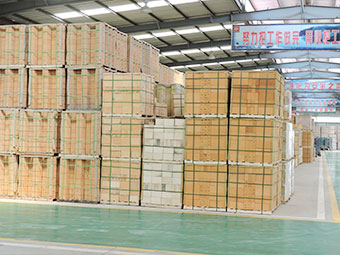
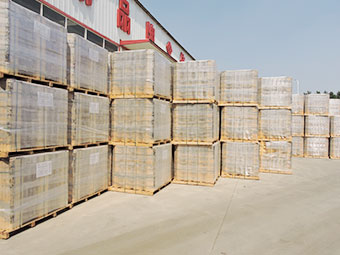
Transportation
★Port of dispatch: Tianjin port; Qingdao port
★Delivery time: According to customer’s demand or two sides negotiate
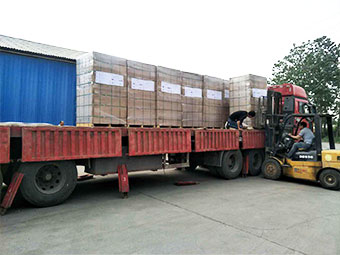

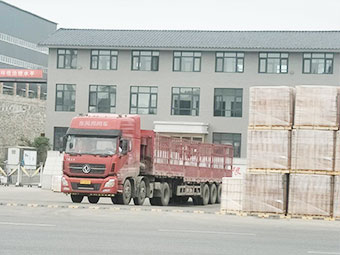
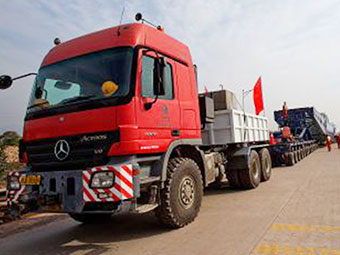
We provide you
★Timely response: Timely response to your inquiry within 24 hours and provide solution.
★Competitive Price: Make the products competitive in your market.
★Free sample: Free sample are offered, trial order are accepted for quality evaluation.
★Strict quality control: We set Quality Management System, from the raw material to finished products, produce high quality products according to chemical & physical specifications strictly to satisfy customers’ needs.
★Fast delivery time: Within 3-30 days according to your quantity after receiving your advance payment.
★ Professional services: Provide pictures from order to delivery. Inspect report by our country’s designated authority and oversea services if necessary.
We are here for you!

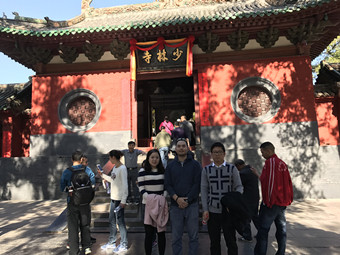
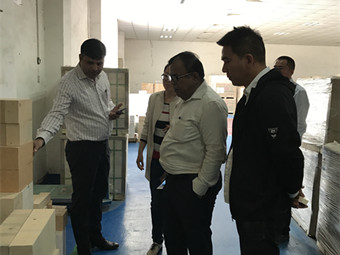
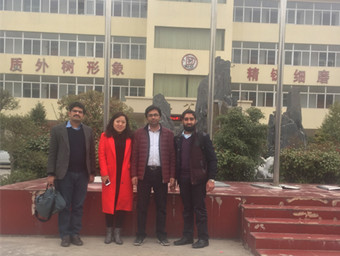
Certification: (ISO 9001:2015)
Please Feel free to give your inquiry in the form below. We will reply you in 24 hours..