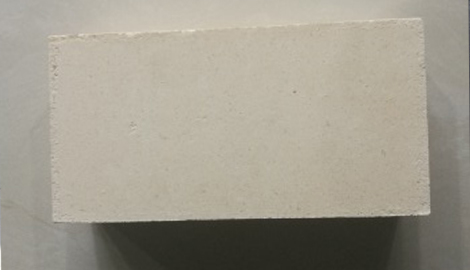
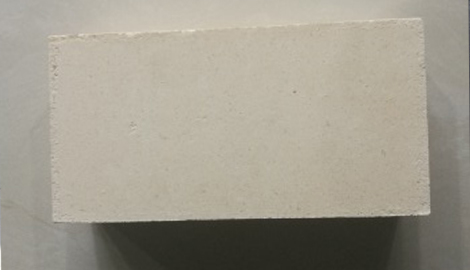
China Manufacturer Dense Sintering Zircon Corundum Bricks
Model Number:
Certification:
Minimum Order Quantity:
zircon corundum refractory brick for steel furnace
Sintered AZS bricks are made of zircon and alumina as the main raw materials, and pre-synthesized materials are used as aggregates. Since the billet is an inert material, it is not effective to increase the molding pressure to increase the density of the product. The increase in the number of presses of large products may also lead to uneven cracking and density. It is necessary to adjust the critical particle size composition, add the composite binder and a small amount of TiO2. , MgO combustion aid and strengthening sintering to achieve the purpose of dense sintering.
The production principle is based on the solid phase reaction between ZrSiO4-Al2O3:
3Al2O3+2ZrSiO4→3Al2O3·2SiO2+2ZrO2
This reaction is an irreversible reaction and is also referred to as "in situ reaction". Due to the large volume effect in the reaction sintering process, resulting in deformation and cracking of the green body, only the pre-synthesized zirconium mullite aggregate, combined with sintered or fused corundum raw materials, can produce mullite, oblique zircon and corundum three-phase. Materials are superior to two-phase materials in terms of strength and thermal shock resistance. The microstructure of the sintered AZS brick is characterized by the uniform distribution of fine oblique zircon particles between the main crystalline phase mullite and corundum.
The electrofusion and AZS bricks are made by casting AZS clinker, scrap or recycled brick (clearing the adhered glass), adding a small amount of kaolin or alumina as a binder. When heated to a high temperature, the fused AZS aggregate exuded the glass phase and the binder to form mullite, which promotes sintering of the article. The peritectic reaction of the glass phase and the crystalline phase in the fused AZS aggregate also forms mullite. At this time, the mullite and ZrO2 are wrapped and wrapped, which contributes to the sintering of the AZS particles of different grades. The use of melt-cast AZS aggregates as "self-sintering" is the basic principle for the production of re-bonded AZS bricks.
The microstructure changes of high temperature firing and electrofusion combined with AZS bricks are mainly:
1 The coarse-grained glass phase exudes to the surface of the particle and reacts with Al2O3 to form a mullite shell to close the exudation channel so that the peritectic reaction proceeds inside the particle;
2 The molten-cast AZS powder glass phase reacts with the active Al2O3, and the matrix is mullite. Combined with the AZS brick microstructure, it has the structural characteristics of dense combination of mullite and corundum oblique zircon co-crystal.
Performance of sintered zircon bricks
In industrial production, in order to reduce costs and improve economic efficiency, sintered zircon bricks have been widely used in the manufacture of sintered zircon bricks. The crystal of zircon (ZrSiO4) is a tetragonal crystal, and the crystal form is usually in the shape of a quadrangular prism. The colors are reddish purple, brown, yellow, gray, and the like. The theoretical composition of zircon is ZrO2: 67.23%, SiO2: 32.77%. Zircon has a melting point of 2420 ° C, a density of 4.6 to 4.7 g/cm 3 and a Mohs hardness of 7.5.
The zircon raw material used for the manufacture of zircon bricks requires a purity of 98% to 99%, wherein the content of ZrO2 should be greater than 63%, and the lower the impurity content, the better. When manufacturing a product, the pure zircon fine powder is first pressed into a compact, calcined at about 1600 ° C, then crushed, molded, and finally fired. Zircon is slowly dissociated from 1540 ° C, and dissociates rapidly from 1750 ° C. At 1870 ° C, the dissociation amount reaches 95%, and the dissociation products are monoclinic zirconia and silica glass. As the dissociation progresses, the variant expansion of zirconia also gradually becomes significant. Due to this feature, the final firing temperature of zircon bricks does not exceed 1600 °C. According to the volume change of the zircon body during the firing process, the temperature rise rate below 600 ° C should be slow to facilitate the removal of moisture and organic matter in the body; between 600 and 1200 ° C, sintering has not yet begun. The temperature rise can be accelerated. Between 1200 and 1500 ° C, the green body undergoes severe shrinkage, so the heating rate should be slow. When molding zircon bricks by molding, it is necessary to add appropriate flux and mineralizer. An example of the ingredients is: 40% fused zircon pellets, 40% zircon sand, 20% zircon powder, and a small amount of fluoride. Using dextrin as a binder, it is molded under high pressure. The performance of this brick is shown in Table 1.
Because zircon is cheaper than zirconia, and it is easy to obtain natural raw materials, it does not change in structure, has low linear expansion coefficient and good thermal shock resistance, so it is a valuable refractory material. The zircon brick can be used as a crucible for smelting lead, antimony and other metals and alloys thereof, cast steel ladle lining bricks, nozzle bricks, and containers for melting alkali-free glass and molten pool bricks.
Production capacity: Our factory actively response to government environmental protection policy, we designed and built the fully automatic controlled high temperature gas tunnel kiln (1700℃), and got capacity of annual output 70,000 tons of high quality refractory products.



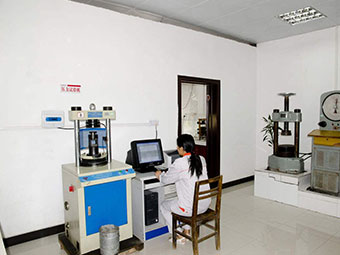
Packing details:
★Bricks: Fumigated wooden pallet with log paperboard covered and stainless steel band strapping, the whole outside is wrapped with thermoplastic film. Or carton packaging.
★Wooden pallet size: usually 92*92cm (standard brick)
★Castable: Ton bag with rain film and 25kg bags inside
★Or according to customer’s requirements
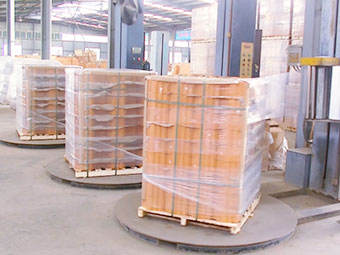
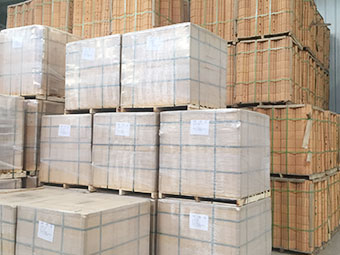
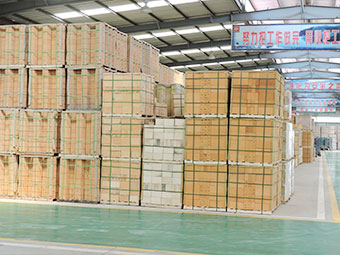
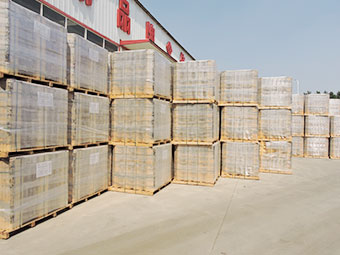
Transportation
★Port of dispatch: Tianjin port; Qingdao port
★Delivery time: According to customer’s demand or two sides negotiate
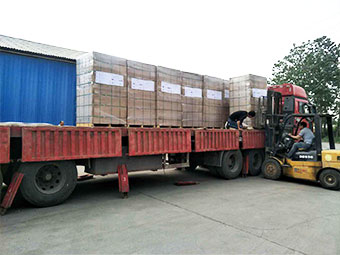

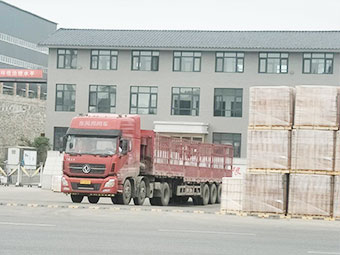
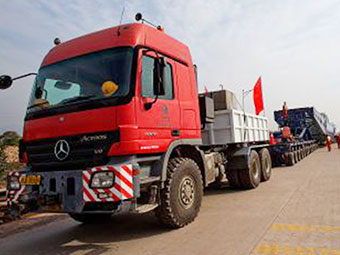
We provide you
★Timely response: Timely response to your inquiry within 24 hours and provide solution.
★Competitive Price: Make the products competitive in your market.
★Free sample: Free sample are offered, trial order are accepted for quality evaluation.
★Strict quality control: We set Quality Management System, from the raw material to finished products, produce high quality products according to chemical & physical specifications strictly to satisfy customers’ needs.
★Fast delivery time: Within 3-30 days according to your quantity after receiving your advance payment.
★ Professional services: Provide pictures from order to delivery. Inspect report by our country’s designated authority and oversea services if necessary.
We are here for you!

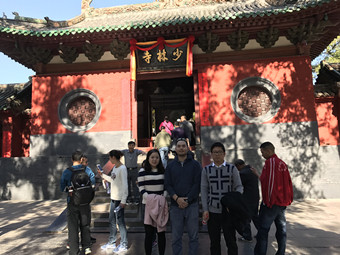
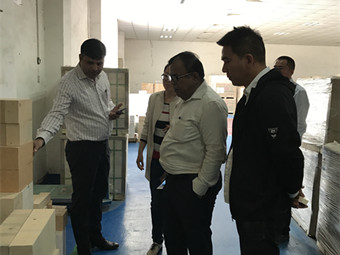
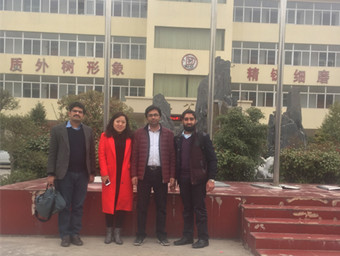
Certification: (ISO 9001:2015)
Please Feel free to give your inquiry in the form below. We will reply you in 24 hours..