Analysis on production and application of sintering and electric melting Fe Al spinel raw materials
2021-04-20 08:33:31
Due to a series of environmental pollution problems caused by the change of chromium price during the high temperature operation of magnesia chrome brick in the firing zone of cement rotary kiln (in the case of more calcium, sodium and potassium in the thermal medium, the amount of Cr3 + converted into Cr6 + increases sharply), magnesia chrome brick directly bonded in the firing zone of cement rotary kiln has been widely replaced by magnesia chrome brick, magnesia alumina spinel brick and magnesia alumina spinel brick, and magnesia dolomite brick is easy to hang The magnesia alumina spinel brick has good corrosion resistance and thermal shock stability, but the poor performance of hanging kiln skin leads to unstable service cycle, which has been stopped in the upper and lower transition zone of rotary kiln; The magnesia iron alumina spinel brick not only has a good performance of hanging kiln skin, but also has room temperature and high temperature performance, especially the thermal shock stability, which is superior to the direct bonded magnesia chrome brick. It is suitable for the harsh requirements of large kilns and new kilns, and its service life is more than 10 months.
An important raw material for producing magnesia alumina spinel brick is ferrite alumina spinel. Ferrite alumina spinel is a natural mineral, which is made of bauxite mudstone rich in iron by high temperature metamorphism. It is black crystal with hardness of 7.5 and density of 3.95 ~ 4.39g · cm-3. But it is rare in nature. It is usually synthesized from rolled steel sheet and alumina by sintering and electrofusion. In the early stage, the high density, low apparent porosity and high spinelization rate of fused Fe Al spinel made it easy to improve the bulk density of products and ensure the quality of products, which became the first choice for the production of Fe Al spinel brick. In recent years, with the improvement of the process, the synthesis of Fe Al spinel by sintering method has been popularized rapidly.
In this paper, through the analysis of the products synthesized by fused raw materials and sintered materials of Fe Al spinel, the main differences between the two raw materials and the practical application effect are found out.
1. Comparison of the properties of the products made of fused Fe Al spinel and sintered material
1.1 raw material performance index
The performance indexes of fused and sintered Fe Al spinel are shown in Table 1.

Table 1 performance index of fused and sintered Fe Al spinel
1.2 basic production process
The brick production is divided into Grade A and grade B. grade A is made of fused alumina spinel (the same below). Grade B is made of sintered alumina spinel instead of fused alumina spinel with the same weight (the same below). The addition amount and particle size ratio of Grade A and grade B medium and high purity magnesia and other raw materials are unchanged. Sulphite pulp waste liquor is used as the binder, which is used in a 2000t double cavity LS automatic hydraulic press Molding, drying in 110 ℃ dryer for more than 12 hours, and sintering in high temperature tunnel kiln at 1650 ℃ for 4.5 hours.
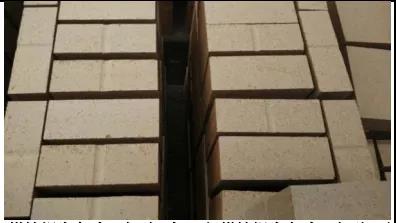
Fig. 1 photos of A-grade Mafia production Brick (left column) and B-grade Mafia production Brick (left column) after being fired out of the kiln
No matter from the appearance or the size change after burning, there is little difference between Grade A and grade B bricks, and it is difficult to distinguish them.
2 test results
The comparison of performance indexes between Grade A and grade B magnesia alumina spinel bricks is shown in Table 2. Through the comparison of conventional properties, it can be found that the bulk density and room temperature compressive strength of grade B Fe Al spinel products are slightly lower than those of Grade A, and the apparent porosity is slightly increased. The softening temperature under load and thermal shock resistance are similar, and there is no obvious difference in chemical composition. This is because the bulk density and apparent porosity of sintered Fe Al spinel are smaller than those of the raw materials, which directly affect the bulk density, apparent porosity and compressive strength of the products. Because the difference is very small, the B-grade spinel products can fully meet the construction and use requirements of large cement rotary kiln firing zone.
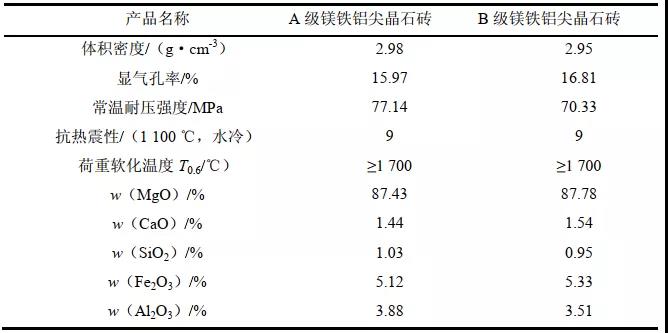
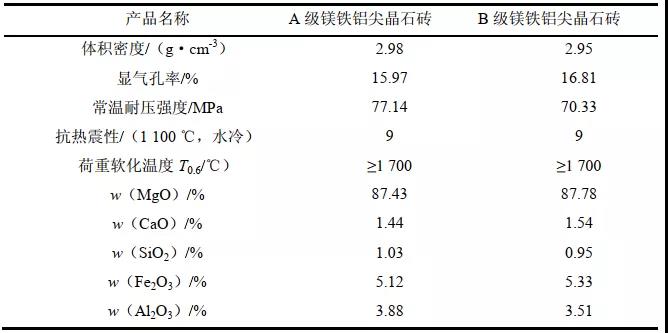
Table 2 Comparison of performance indexes of Grade A and grade B magnesia alumina spinel bricks
The grade A and grade B magnesia iron aluminum spinel bricks were cut into two pieces of 80mm × 80mm × 65mm (as a group). According to the proportion of new raw cement: kiln skin = 7:3, mix evenly (particle size ≤ 0.088mm), use sanmingzhi method to spread the mixture as interlayer in the middle of each group of sample blocks, and add 30g for each group. Put the sample block filled with mixture into the reburning furnace and keep it at 1500 ℃ for 360min. After cooling, take it out and separate it. Observe the layer of the clip, as shown in Fig. 2 and Fig. 3.

Fig. 2A magnesia alumina spinel brick hanging kiln skin test (left is the lower brick sample, right is the upper brick sample)
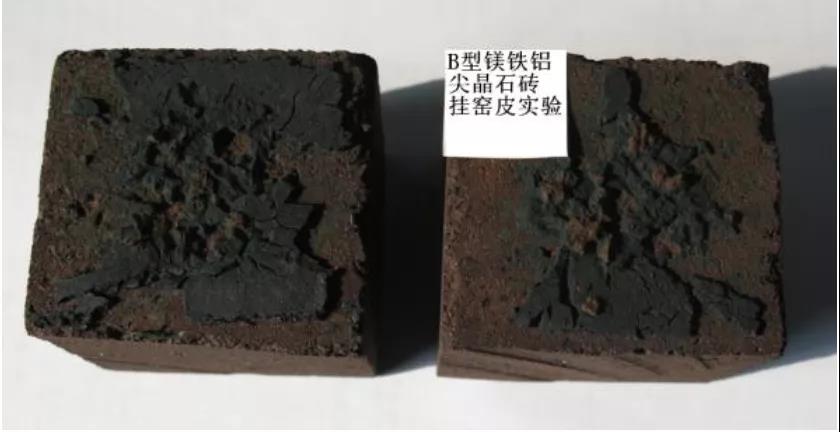
Fig. 3B magnesia alumina spinel brick hanging kiln skin test (left is the lower brick sample, right is the upper brick sample)
According to the samples separated from the hanging kiln skin test, it is easy to hang the kiln skin on both A-level and B-level MgFe al spinel bricks. From the amount of adhering kiln skin on the upper brick sample, it can be seen that the B-level MgFe al spinel bricks hang a little more than A-level ones, and the adhesion is more firm. Because there is no obvious difference in chemical composition between Grade A and grade B magnesia alumina spinel brick, grade B magnesia alumina spinel brick has large apparent porosity, and the amount of powder penetrating into the surface layer of brick body is large, so it is easier for the surface layer to react to form a firm kiln skin.
3. Application effect
After batch marking, Grade A and grade B magnesia alumina spinel bricks were laid on the firing zone of 5000t / d cement kiln. After 11 and a half months of operation, the residual bricks of 220mm grade A and grade B magnesia alumina spinel products were 140 ~ 160mm, and the strength within 100 mm of the end was still high, and the wear and spalling area was relatively uniform. The residual bricks of Grade A and grade B magnesia alumina spinel products were compared It is found that the wear amount is very close, and the difference is not big. It can be inferred that the service life of the two is very close, and there is no big difference.
4 Conclusion
Although the bulk density, room temperature compressive strength and apparent porosity of magnesia alumina spinel brick produced by iron alumina spinel sintering material are slightly lower than those produced by electric melting material, the thermal shock stability and load softening temperature are still better, and it is easier to hang the kiln skin, which can fully meet the requirements of construction and use. The service life of magnesia alumina spinel brick is not different from that synthesized by electric melting material It's the raw material of our company.
Relevant information
-
Thermal storage alumina balls
The Thermal storage alumina ballsis made of industrial alumina and refractory kaolin as the main raw materials through scientific formula, forming and high-temperature calcination.Thermal storage alumina ballss are divid··· -
Anti-stripping high alumina brick
Use description of Anti-stripping high alumina brick1. Anti-stripping high alumina brick has a good application in low temperature parts such as large and medium-sized cement precalciner, kiln smoke chamber, indoor decom··· -
Anti-stripping high alumina bricks
Anti-stripping high alumina bricks are made of high alumina bauxite clinker, mullite, kyanite, zircon sand, and binder after granulating and powdering processes, mixed in a certain proportion, pressed into shape, and fir··· -
silica hot repair refractory
Performance index of silica hot repair refractoryThe material is a kind of plastic unshaped refractory material, its main component is SiO2, it is made of special clinker and various binders and additives, and it is proc···