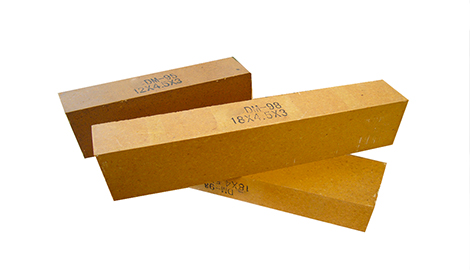
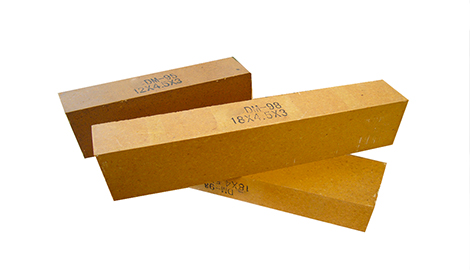
Magnesium brick product introduction
An alkaline refractory material having a magnesium oxide content of 90% or more and a periclsite as a main phase.
Generally, it can be divided into two categories: sintered magnesia brick (also known as burnt magnesia brick) and chemically combined magnesia brick (also known as non-burned magnesia brick). Magnesia bricks with high purity and high firing temperature are called direct-bonded magnesia bricks because of the direct contact of the magnesite grains. The bricks made of fused magnesia are called electrofusion and recombined magnesia bricks.
An alkaline refractory product containing periclase as the main phase. The product has the characteristics of high temperature mechanical strength, good slag resistance, strong corrosion resistance and stable volume at high temperature.
Magnesia bricks have high refractoriness, good resistance to alkaline slag, high starting temperature of load softening, but poor thermal shock resistance. The sintered magnesia brick is made of brick and magnesia bricks. After being pulverized, compounded, kneaded and formed, it is fired at a high temperature of 1550 to 1600 ° C. The high-purity product has a firing temperature of 1750 ° C or higher. The non-casting magnesia brick is made by adding a suitable chemical binder to the magnesia, mixing, forming and drying.
Mainly used in steelmaking alkaline open hearth furnace, electric furnace bottom and furnace wall, permanent lining of oxygen converter, non-ferrous metal smelting furnace, high temperature tunnel kiln, calcined magnesia brick and cement rotary kiln lining, heating furnace bottom and furnace wall, Glass kiln regenerator lattice bricks, etc.
type |
|
|
|
CCS |
RUL(℃) ≥ |
TSR |
|||
MgO |
SiO2 |
CaO |
|||||||
|
MZ-90 |
90 |
20 |
2.90 |
50 |
1500 |
10 |
||
MZ-92 |
92 |
3 |
2.5 |
18 |
2.92 |
55 |
1550 |
10 |
|
MZ-95 |
95 |
2.5 |
2.0 |
18 |
2.95 |
60 |
1600 |
10 |
|
MZ-97 |
97 |
1.2 |
1.5 |
17 |
3.00 |
70 |
1650 |
10 |
|
|
DMZ-96 |
95.5 |
2.0 |
1.5 |
17 |
2.95 |
65 |
1600 |
8 |
DMZ-97B |
96.5 |
1.5 |
1.2 |
16 |
3.05 |
70 |
1700 |
8 |
|
DMZ-97A |
96.8 |
1.5 |
1.2 |
16 |
3.10 |
70 |
1700 |
8 |
|
DMZ-98B |
97.3 |
1.2 |
1.2 |
15 |
3.10 |
80 |
1700 |
8 |
|
DMZ-98A |
97.5 |
1.0 |
1.2 |
15 |
3.15 |
80 |
1700 |
8 |
1, the main performance of magnesium brick
Refractoriness
Because the melting point of periclase (MgO) crystals is very high, up to 2800 ° C, the refractoriness of magnesia bricks is the highest in general refractory bricks, usually above 2000 ° C.
Slag resistance
Magnesia brick is an alkaline refractory material. It has strong resistance to alkaline slag such as CaO and FeO. It is usually used as a masonry material for alkaline smelting furnaces, but its resistance to acid slag is very poor. Magnesia bricks are not in contact with acidic refractories and they are eroded by chemical reactions at temperatures above 1500 °C. Therefore, magnesia bricks cannot be mixed with silica bricks.
Thermal stability
Magnesia bricks have poor thermal stability and can only withstand water cooling 2 to 8 times, which is a big disadvantage.
Volume stability
The thermal expansion coefficient of magnesia bricks is large, and the coefficient of linear expansion between 20 and 1500 °C is 14.3×106. Therefore, sufficient expansion joints should be left in the process of bricklaying.
Thermal conductivity
The thermal conductivity of magnesia bricks is several times that of clay bricks. Therefore, the outer layer of the furnace brick masonry should generally have sufficient insulation to reduce heat loss.
2. Application of Magnesia Brick Magnesia brick is widely used in the metallurgical industry.
In the steelmaking industry, it can be used to build alkaline flat furnace bottom and furnace wall, top blow converter lining, electric arc furnace wall, furnace bottom, soaking furnace and heating furnace bottom, and iron furnace lining. In the non-ferrous metallurgical industry, it is used to build copper, nickel, lead blast furnace hearth, front bed, refined copper reverberatory furnace, ore electric furnace inner village.
The refractoriness of the magnesia brick is as high as 2000 ° C or higher, and the load softening temperature does not vary greatly depending on the melting point of the binder phase and the liquid phase produced at a high temperature. Generally, the load-softening start temperature of the magnesia brick is between 1520 and 1600 ° C, and the high-purity magnesia brick has a heavy softening start temperature of up to 1800 ° C.
In ordinary magnesia bricks, as a combination, it is generally a low-melting silicate phase such as calcium forsterite and magnesia, although the calcite crystals constituting the magnesia have a higher melting point, but melt at about 1500 ° C. The silicate phase exists, and its liquid phase has a small viscosity at high temperature. Therefore, it reflects that the load temperature of the ordinary magnesia brick is not much different from the collapse temperature, but it is quite different from the refractoriness. The loading softening start temperature of high-purity magnesia bricks can reach 1800 °C, mainly because the combination of the magnesite grains is forsterite or dicalcium silicate, and the melting temperature of the eutectic formed by the MgO is high. The lattice strength between the crystals is large and the plastic deformation at high temperatures is small, and the crystal particles are well bonded.
The linear expansion rate of magnesia bricks at 1000-1600 °C is generally 1.0%-2.0%, and is similar or linear. In refractory products, the thermal conductivity of magnesia bricks is second only to carbon-containing bricks, which increases with temperature. reduce. Under the condition of water cooling at 1100 °C, the thermal shock frequency of the magnesia brick is only 1 or 2 times. Magnesia bricks have strong resistance to CaO and ferric alkaline slag, but have weak resistance to acidic slags such as SiO2.
Therefore, it cannot be directly contacted with silica bricks during use, and is generally separated by neutral bricks. At normal temperature, the conductivity of magnesia bricks is very low, but at high temperatures, its conductivity cannot be ignored. The performance of magnesia bricks is greatly different due to the different raw materials, production equipment and process measures.
Magnesia bricks are widely used in steelmaking lining, iron alloy furnaces, mixed iron furnaces, non-ferrous metallurgical industrial furnaces, limestone kiln for building materials, and lattice storage of glass industrial regenerators due to their high temperature performance and strong resistance to alkaline slag. High temperature calcining kiln and tunnel kiln for heat exchanger and refractory industry.
Production capacity: Our factory actively response to government environmental protection policy, we designed and built the fully automatic controlled high temperature gas tunnel kiln (1700℃), and got capacity of annual output 70,000 tons of high quality refractory products.



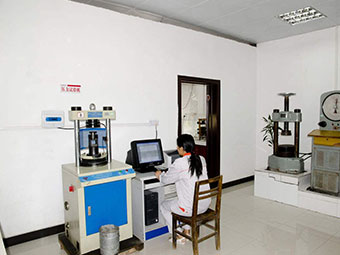
Packing details:
★Bricks: Fumigated wooden pallet with log paperboard covered and stainless steel band strapping, the whole outside is wrapped with thermoplastic film. Or carton packaging.
★Wooden pallet size: usually 92*92cm (standard brick)
★Castable: Ton bag with rain film and 25kg bags inside
★Or according to customer’s requirements
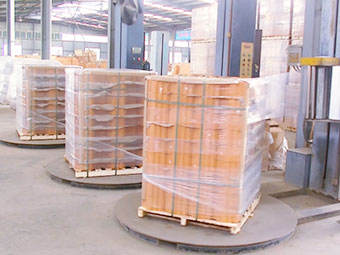
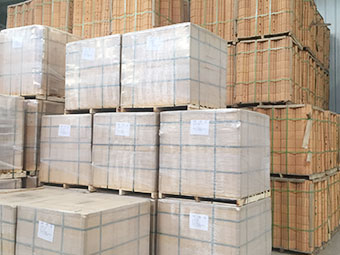
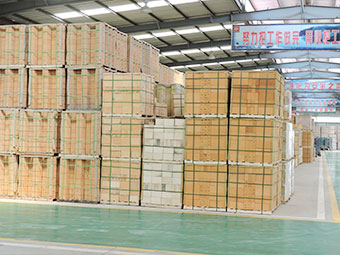
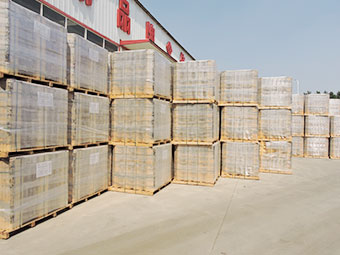
Transportation
★Port of dispatch: Tianjin port; Qingdao port
★Delivery time: According to customer’s demand or two sides negotiate
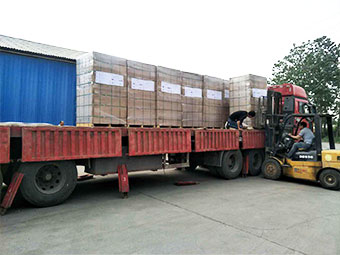

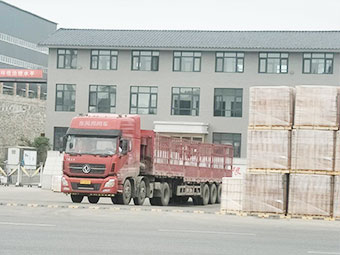
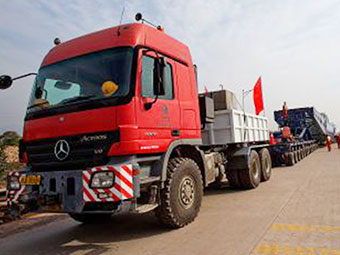
We provide you
★Timely response: Timely response to your inquiry within 24 hours and provide solution.
★Competitive Price: Make the products competitive in your market.
★Free sample: Free sample are offered, trial order are accepted for quality evaluation.
★Strict quality control: We set Quality Management System, from the raw material to finished products, produce high quality products according to chemical & physical specifications strictly to satisfy customers’ needs.
★Fast delivery time: Within 3-30 days according to your quantity after receiving your advance payment.
★ Professional services: Provide pictures from order to delivery. Inspect report by our country’s designated authority and oversea services if necessary.
We are here for you!

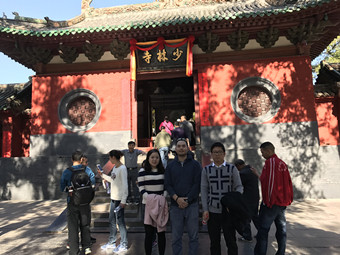
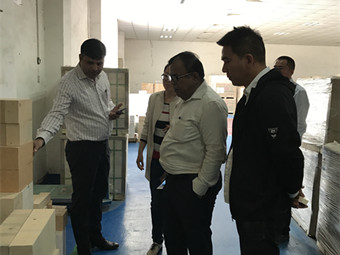
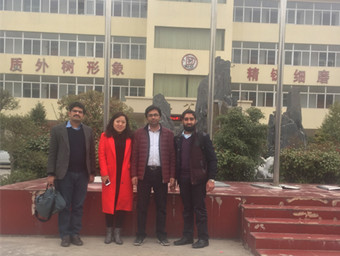
Certification: (ISO 9001:2015)
Please Feel free to give your inquiry in the form below. We will reply you in 24 hours..